Table of Content
1 Challenge #1 No Risk-Based Approach for Maintenance
2 Challenge #2 Maintenance Systems Are Not Optimally Used
3 Challenge #3 Maintenance Plans Are Not Regularly Updated
4 Challenge #4 No Adequate Training Platform and Programs
5 Challenge #5 Impact of Lubricants is Not Considered Prominently
6 Challenge #6 Poor Classification for Production and Non-Production Equipment
7 Challenge #7 No Documentation for Maintenance Activities
8 Challenge #8 Advanced Maintenance Management Tools are Overlooked
9 Challenge #9 Equipment Related Documentation is Not Easily Accessible
10 Challenge #10 Maintenance Is Not Considered Right from Equipment Purchase
The Bottom Line
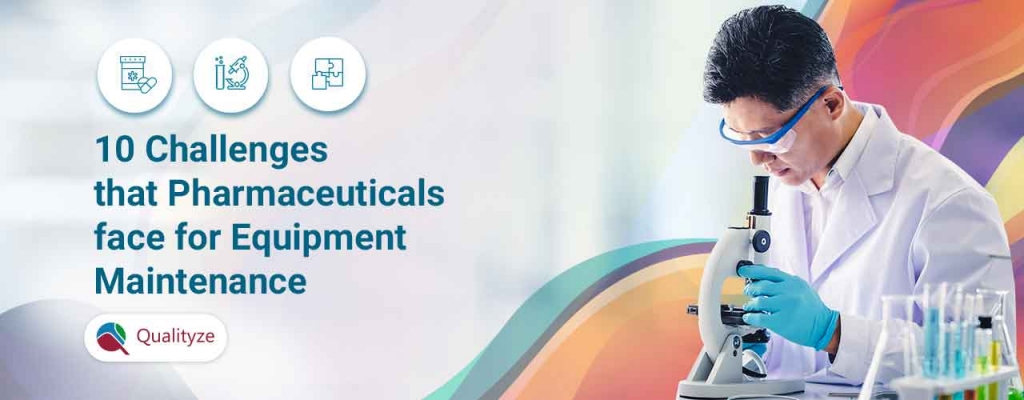
Pharmaceutical is among the industries that have complex processes. It continuously requires new strategies to improve the ongoing operations, achieve business goals, and maintain competitiveness. One of the common mistakes they make while developing business strategies is not considering equipment maintenance. That’s why pharmaceutical companies face numerous challenges for their equipment maintenance activities.
It’s high time for the pharmaceutical industry to adopt a powerful maintenance management system that can help them overcome the equipment maintenance challenges they face with the traditional techniques. It will also help them save costs on production/equipment failure.
In this post, we will look at the ten common challenges that Pharmaceutical companies face for equipment maintenance and the most recommended solutions to overcome these challenges.
10 Challenges that Pharmaceutical Companies Face for Equipment Maintenance
Challenge #1 No Risk-Based Approach for Maintenance
In the pharmaceutical industry, you cannot treat every equipment equally, especially when it comes to maintenance. The best pharmaceuticals approach is using a risk-based approach for equipment maintenance that includes classification of equipment based on their impact and role in the overall product quality.
However, equipment classification and managing their maintenance becomes challenging with the traditional paper-based process management system. You can overcome this challenge using an integrated maintenance management solution that allows you to create, manage, and track different equipment maintenance activities without any hassles. The next-generation software solutions are designed to cater to all your compliance needs, including developing and implementing a risk-based approach.
Challenge #2 Maintenance Systems Are Not Optimally Used
Computer-based maintenance systems are given more preference these days to manage maintenance related tasks since they simplify documentation, scheduling, and tracking of equipment maintenance – for both single-site and multi-site. But this requires pharmaceutical companies to go the extra mile to research the right maintenance systems, preferably validated ones.
Validated CMMS may cost you a bit higher, but it is worth all the ease you will experience during audits and regulatory inspections. It will not be possible with unvalidated CMMS. Remember, if you think validation is not something you can afford, you cannot make optimal use of the maintenance system.
Challenge #3 Maintenance Plans Are Not Regularly Updated
Buying new equipment strikes with a sense of excitement about improved performance and speed. The majority of the organizations forget the very basic fact that the new equipment will also need regular maintenance for longer life and smooth functioning. And, they don’t update the maintenance plans as per the new members of the production family.
Pharmaceutical companies need to use the Electronic Document Management System that simplifies managing all sorts of documents related to the existing and new equipment – be it their maintenance plans, frequency, or any other compliance-related documentation. An EDMS enables enterprises to keep their critical documents regularly updated, keeping track of the changes done.
Challenge #4 No Adequate Training Platform and Programs
Is your maintenance staff know the impact of changing a single setting in the equipment they use every day? Do they understand the compliance? Do they consider quality assurance? You must ensure that your maintenance staff is trained on all the required tools and platforms by providing them timely and relevant training.
The traditional training management system is not successful anymore. You must implement a powerful Training Management System that can help you create multiple training schedules for different departments, job functions, and locations without any hassles. You can easily find the training management systems on which you can make document-based and instructor-led training programs.
Challenge #5 Impact of Lubricants is Not Considered Prominently
Ask any pharmaceutical manufacturers “what impact lubricants make on the product quality,” and they will be puzzled about what to say or answers. It happens because the impact of lubricants is generally not considered as prominently as it should be. You must keep equipment lubricant impact listed on the checklist to ensure no quality metrics left unattended.
Even if the old lubricants are changed with the new options available in the market for better equipment performance, you must document it. It will become easy for you to identify errors much before the product release, preventing any catastrophic event. You can use an integrated quality management system that automatically records all the data you enter in the forms. Such an organized approach is often recommended under regulatory standards.
Related Article - The Rising Importance of Supply Chain Management in the Pharmaceutical Industry: From Labs to Lives
Challenge #6 Poor Classification for Production and Non-Production Equipment
In addition to more giant machines and equipment, there are numerous spare parts and other small devices that are not considered for maintenance. Pharmaceutical companies must have proper production and non-production equipment to prioritize their maintenance schedules.
You can utilize quality management software to align your processes and assign them to the right people to achieve your business goals faster than ever. For example, if you want approval for critical maintenance tasks, you can specify approver(s) using the quality management software. It will automatically send alerts to the involved parties for quick approvals.
Challenge #7 No Documentation for Maintenance Activities
Documentation of all the maintenance activities – the procedure, work instruction, and policies, has recently gained traction due to the stringent auditing and compliance standards. Many enterprises rely on paper-based systems, which are not efficient and compliance-friendly.
Hence, pharmaceutical companies need a comprehensive document management system to create, manage and track standardized documents for every maintenance activity. It ensures a consistent flow of information throughout the organization, keeping all your team members on the same page. Documenting the critical activities and the FDA often recommends their objective evidence to the best practice for the regulated industries.
Challenge #8 Advanced Maintenance Management Tools are Overlooked
Though it looks easy to do things the way you have always been doing, especially with the pressure of meeting the targeted stuff, it is advisable to adopt the newest tools and methodologies to execute the tasks efficiently, smartly, and securely. It also helps you comply with GMP and the customer requirements, continuously improving product and process quality.
Therefore, pharmaceutical companies should adopt new tools and technologies to streamline their critical processes in the most efficient manner. Advanced quality management tools also leverage accuracy and consistency in processing business essential information without any hassles. Would you still overlook new tools for managing your quality processes?
Challenge #9 Equipment Related Documentation is Not Easily Accessible
Accessibility is another core issue that pharmaceutical companies when it comes to equipment-related documentation. This often results in a lack of traceability and impact decision making drastically. But you can overcome it quite easily with a cloud-based quality management system.
A cloud-based quality management system increases accessibility, traceability, and security to manage critical documentation easily. You can also leverage the centralized platform to communicate and collaborate with your team, regardless of their geographical location. The cloud-based systems have completely transformed the way businesses used to manage their critical data.
Challenge #10 Maintenance Is Not Considered Right from Equipment Purchase
Another most common issue for equipment maintenance in the pharmaceutical sector is not considering the maintenance activities right from equipment purchase. Instead, the maintenance activity should be included in the strategic business plans right from the equipment’s purchase.
Maintenance activities managed strategically helps businesses maintain their assets for a more extended period.
You can transform all the challenges mentioned above into excellent opportunities for your businesses in a better, faster, and smarter way by using an integrated maintenance management solution. It will help you manage, control, and track the maintenance activities in a streamlined, compliant, and timely fashion before a missed maintenance causes more significant losses.
One of the highly recommended solutions is Qualityze Maintenance Management Software. Intuitive, configurable, and cloud-based, the software is specifically designed to help an enterprise manage all its maintenance-related activities for both single-site and multi-site operations without any operational issues. It enables you to set up maintenance schedules for different assets on a Yearly, Quarterly, Monthly, Weekly, Daily basis.
It is built on the most powerful, secure, and reliable cloud platform i.e., Salesforce.com. It offers greater flexibility and visibility to manage all the inspection related processes. It comes with great functionalities such as dashboard and reporting, alerts and notifications, watermark, electronic signature, task scheduler, and much more.
Qualityze smarter quality solutions transform your QMS into a quality decision-making engine. Organizations, regardless of their industry focus, can perform quick real-time analysis of quality data with analytics and reporting, prevent miscommunication, implement improvement for mass production, maintain consistency, reduce the overhead expenses, immediately notify quality teams of upcoming Reviews, Audits, Training sessions, Follow-ups, Actions, Approvals, and Change Implementations, and much more.
The Bottom Line
Regular maintenance activities help enhance the performance of your assets, decreasing their downtime and overall maintenance costs. It is essential that you manage, track, and control them in a standardized manner using the powerful maintenance management software like Qualityze.
Want to know more about Qualityze EQMS Suite? Get in touch with our customer success team at 1-877-207-8616 or write to us at info@qualityze.com. We will be right there for you.
Share
The Start of Something Amazing.
Request Demo
Products
Industries
Company