Table of Content
1 7 Reasons Why Maintenance Management System Is Important
Reduced equipment downtime and lesser repair requirements
The increased life expectancy of the equipment and machinery assets
Reduced overhead expenses
Timely execution of maintenance activities
Improved safety for your employees
Simplifies the job of maintenance staff
Increased efficiency and sustainability
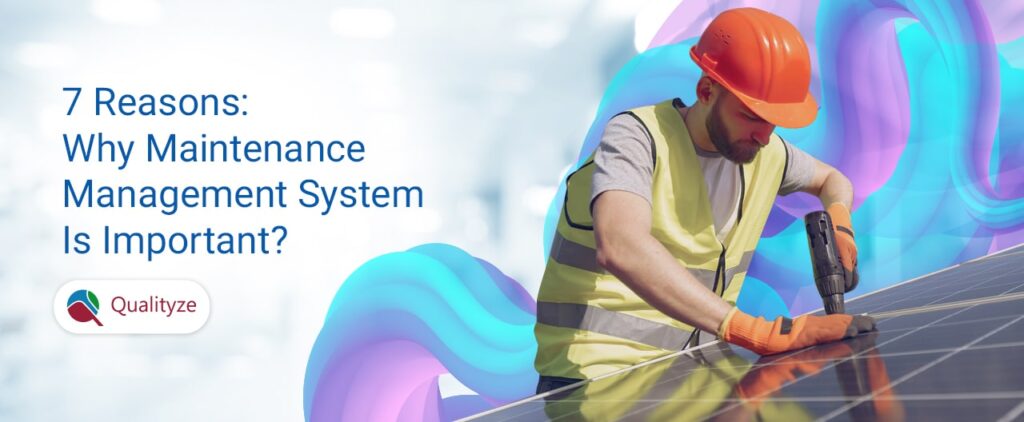
It is ubiquitous to see facility managers reacting to quality issues than taking a proactive approach to preventing them in the first place when it comes to maintaining the equipment and machines they use. The primary reason for the reactive approach is saving money, but businesses often overlook the long-term effects of the same.
So, how would you prefer to go – preventing the problems to avoid any severe consequences or waiting for the expensive surprises to react upon?
The latter may look like an obvious pick since one cannot determine all the issues well in advance. The best hack is to analyze the failure trends to identify preventable quality issues, while for the sudden failures, you can always define some standard actionable steps.
An effective maintenance management system ensures consistent best practices that improve the overall performance and safety of the equipment used in manufacturing and testing the product quality. Furthermore, it will improve the equipment life and eliminate the hassles of unplanned maintenance activities.
Related Article: Here’s the Guide to Build an Effective Maintenance Plan
7 Reasons Why Maintenance Management System Is Important
-
Reduced equipment downtime and lesser repair requirements
You are likely to experience equipment downtime more frequently if they are not maintained regularly. The downtime could further result in production delays and increase the product’s time-to-market. A Maintenance Management Software can help you prevent such circumstances by enabling you to schedule maintenance activities in advance. Timely maintenance of the equipment ensures improved performance, productivity, and safety. And the hassle-free production would result in a better quality product. It is likely to reduce the repair requirements as well. Would you instead spend more time dealing with downtime and repairs or take a proactive approach to prevent such issues in the first place?
-
The increased life expectancy of the equipment and machinery assets
Performing preventive maintenance can help you increase the life of the equipment and machinery assets. When you take care of the maintenance activities on time before they get worse and result in sudden breakdowns and failures, your equipment is likely to function longer than expected. Moreover, you won’t need to invest in the new machinery assets any time soon. A maintenance management software can support your maintenance activities effortlessly. You can easily find cloud-based maintenance management solutions that allow you to set alerts and notifications for the maintenance activities before they are due. Always remember, regular maintenance can improve equipment’s life expectancy.
-
Reduced overhead expenses
As we have already discussed, regular maintenance could save you from sudden equipment failures and downtime. You may not need to spend on new machinery sooner like before. So, you are likely to save overhead expenses due to all such failures and delayed product delivery. Having maintenance management software will also eliminate the need for maintaining paper-based documents such as equipment maintenance records, certificates, and even measurement accuracy. The software can reduce all the administrative activities to a minimum, saving you from unnecessary resources and repair expenditure.
-
Timely execution of maintenance activities
It is yet another common issue when it comes to the execution of maintenance activities. The maintenance team often forgets to perform maintenance activities as scheduled for critical equipment due to a sudden failure or equipment breakdown in some other business unit. This is where the reactive approach can cost you a fortune. On the other hand, maintenance management software can help you take a proactive approach by analyzing all the equipment’s failure and performance trends. Accordingly, you can schedule their maintenance activities at desired time intervals. The software sends alerts to all the team members to plan and execute all the scheduled actions on time.
-
Improved safety for your employees
A missed maintenance is not suitable for any business – not only for increased expenses but also for employee safety. A sudden breakdown or equipment failure could even result in life risks for the employees in the production unit. Therefore, you must build a culture of quality and safety by training your employees on best practices – for managing equipment calibration and maintenance activities. You can also integrate a training and maintenance management system to ensure that your employees are skilled and trained on the safe execution of activities. Moreover, you need not worry about missing maintenance with the use of the right software.
Related Article: How to Manage Equipment Calibration? (Here’s A Simple Solution)
-
Simplifies the job of maintenance staff
Your maintenance staff may face numerous challenges when working with a manual maintenance management system, such as record-keeping, maintaining device history records and their maintenance certificates, performing maintenance activities on time, and much more. A maintenance management software can help you streamline, standardize, and automate all such activities, reducing the workload of maintenance staff so they can focus on more critical activities that contribute to equipment life and performance. In addition, you can easily find software with configurable workflows. It will enable you to create simple workflows for your staff, reducing the overall process cycle time.
-
Increased efficiency and sustainability
Inappropriately maintained equipment isn’t good and safe for a work environment since it involves life-threatening risks for the staff involved. Also, the equipment is likely to use more energy than usual when not maintained timely. The maintenance activities ensure that your equipment is in good operational condition and will pose no risk for the employees’ safety. However, managing maintenance activities manually can be time-consuming and tedious. Therefore, it would be best to implement effective maintenance management software to address repair and maintenance activities, improving the efficiency and sustainability of the machinery.
It is pretty evident from the discussion above that having maintenance management software can be a beneficial deal for your business. But the primary concern here is choosing the right software that can cater to your business-specific compliance requirements.
We have got you covered here! One of the highly recommended maintenance management software is Qualityze. It is built on the most powerful and secure cloud platform – Salesforce.com – to provide the required flexibility, security, and reliability for managing critical maintenance activities in all locations in a hassle-free manner. In addition, it comes with impressive in-built capabilities such as Reports, Dashboards, Audit Trails, Digital Signature, Chatter, and much more.
Related Topic - Maintenance Management: Here are Different Types of Maintenances You Should Know About
Experience the difference in managing maintenance activities and their respective schedules efficiently with Qualityze maintenance management. The result is a longer life expectancy of your equipment, instruments, and devices, essential for product quality and employees’ safety. It is the most hassle-free and straightforward to address maintenance challenges of the modern business era.
If you want to know more about Qualityze Maintenance Management Solution or wish to get a free demo scheduled, get in touch with our customer success team on 1-877-207-8616 or write to us at info@qualityze.com and we will be right there for you.
Share
The Start of Something Amazing.
Request Demo
Products
Industries
Company