Table of Content
1 The Bigger Picture of Visual Problem‑Solving
2 What Is a Fishbone Diagram?
3 What Is Cause‑and‑Effect Analysis?
4 Cause and Effect vs Fishbone Diagram—What’s the difference?
5 When to Use Cause and Effect vs Fishbone Diagram in Quality Management
6 Cause and Effect vs Fishbone Diagram—Which One Wins?
7 Visual Tools for Root Cause Analysis: Comparing Fishbone, Flowcharts, and Cause & Effect Diagrams
Decision Framework—Pick the Right Tool Every Time
10 | Where Software Steps In
FAQs— Cause and Effect vs Fishbone Diagram
Key Takeaways
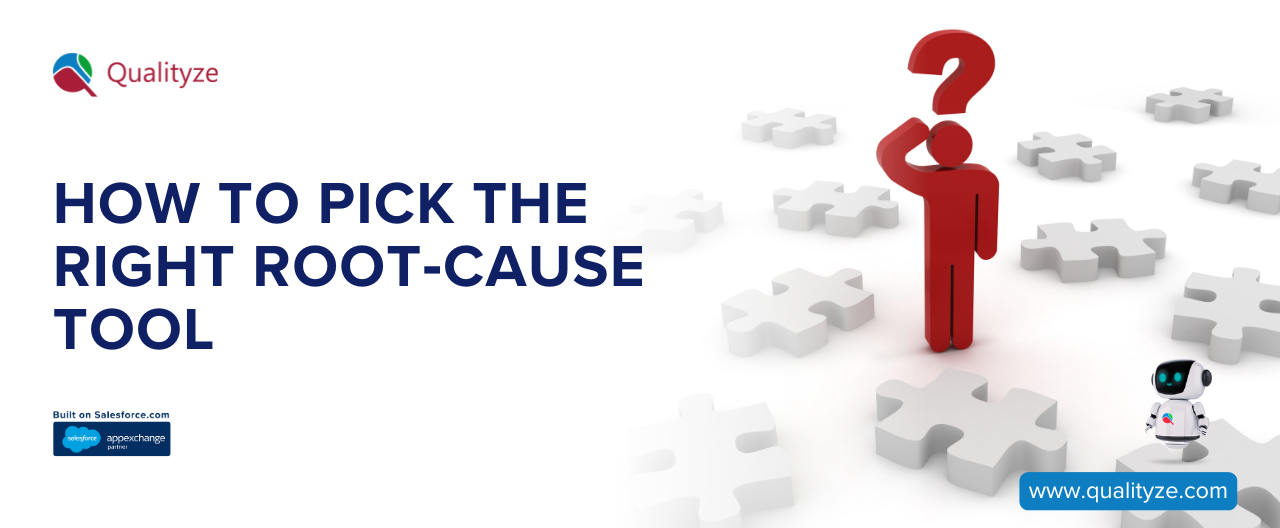
When a defect keeps coming back, the real battle isn’t on the shop floor—it’s in the conference room where you decide which root‑cause tool to use. Pick wrong and you’ll chase symptoms for weeks; choose wisely and scrap, delays, and customer complaints shrink almost overnight. This guide breaks down the essentials of Cause and Effect vs Fishbone Diagram, shows where matrices and flowcharts fit, and gives you a quick‑fire decision framework so your next problem‑solving session starts strong and finishes with data‑backed results.
Why it matters?
Imagine the line stops cold at 3 p.m. Scrap bins fill, the clock ticks, leadership wants the answer before the next shift. If you choose the wrong analysis tool, you’ll drown in sticky‑notes, chasing symptoms instead of causes. A 2023 Lean Six Sigma review found that uncontrolled process variation drives up to 70 % of manufacturing defects—and most of that waste survives because teams' mis‑diagnose the root cause on day one.
This guide clears the fog. You’ll learn exactly when to grab a Fishbone Diagram, when to lean on broader Cause‑and‑Effect (C&E) analysis, and when another visual—like a C&E Matrix or flowchart—will save you hours and mountains of rework.
The Bigger Picture of Visual Problem‑Solving
Before moving on to Cause and Effect vs Fishbone Diagram section, let us first understand the existence of root cause analysis tools, and where it all began.
Root‑cause tools exist because the human brain likes pictures. Kaoru Ishikawa himself put it plainly: “Quality control starts and ends with training.” Training people to think visually short‑circuits groupthink and guesswork, whether you’re running Six Sigma, TPS, or a basic CAPA management. The Fishbone Diagram is one of the Seven Basic Quality Tools—same league as Pareto and control charts. But it isn’t the only game in town. Modern quality teams rotate through a toolbox that also includes the C&E Matrix, scatter plots, and 5 Whys trees. Picking right means matching tool power to problem complexity.
What Is a Fishbone Diagram?
A Fishbone Diagram—also called an Ishikawa Diagram—maps every plausible root cause onto “bones” radiating from a central “spine,” all pointing to the effect (the problem statement) at the fish’s head. Originally built around the “6 Ms” (Man, Machine, Method, Material, Measurement, Mother Nature), modern versions swap in the “8 Ps” or whatever categories fit your industry. The magic? You force the team to categorize on the fly, so brainstorming stays structured instead of spiraling.
Quick win: Set a 20‑minute timer. Demand at least three causes per major bone before the buzzer. You’ll surface hidden assumptions fast.
What Is Cause‑and‑Effect Analysis?
Cause‑and‑Effect Analysis is the broader discipline of linking outcomes to origins. Think of it as the umbrella under which several tools live: Fishbone, 5 Whys, Pareto, scatter plots, even Design of Experiments. The cycle is simple:
-
Define the effect in measurable terms.
-
Brainstorm causes using a structured tool.
-
Validate with data—run a C&E Matrix, test correlations, or do a pilot fix.
Where the Fishbone shines at idea generation, the wider C&E process keeps you honest once whiteboard ink dries.
Cause and Effect vs Fishbone Diagram—What’s the difference?
Here is quick summary of differences between fishbone and cause and effect diagram
Dimension |
Fishbone Diagram (the visual) |
Cause‑and‑Effect Analysis (the process) |
What It Means for You |
Scope |
Snapshot of possible causes |
End‑to‑end journey from effect to verified root |
Use fishbone as step 1 |
Time to Build |
10‑30 minutes |
Hours to weeks (data collection) |
Start with fishbone, finish with data |
Depth |
Breadth > depth |
Depth & statistical proof |
Pair them for speed + certainty |
Best Use |
Rapid team brainstorming |
Complex problems needing prioritization |
Blend both on chronic issues |
When to Use Cause and Effect vs Fishbone Diagram in Quality Management
Scenario |
Best Pick |
Why |
Unexpected spike in scrap, obvious time pressure |
Fishbone |
Fast, visual, engages line team |
Recurring customer complaint with multiple variables |
Full C&E analysis |
Needs data validation & weighting |
Regulatory CAPA with deadline |
Fishbone → C&E Matrix |
Brainstorm, then score causes by risk |
Design‑stage FMEA prep |
C&E Matrix first |
Quantifies impact before design freeze |
Cause and Effect vs Fishbone Diagram: A beverage plant saw fill‑level rejects jump from 0.5 % to 2 %. In a 15‑minute fishbone, the team listed “valve wear,” “operator change,” and “temperature drift.” A follow‑up C&E Matrix scored temperature drift highest; data loggers confirmed 3 °C swing. A $500 thermostat fix dropped rejects below 0.3 % in 48 hours.
Cause and Effect vs Fishbone Diagram—Which One Wins?
A Cause-and-Effect (C&E)—sometimes called an X‑Y or prioritization matrix—lists potential causes on rows, key effects on columns, and assigns weightings (1–10). Totals highlight the causes most worth attacking.
Strength |
Fishbone |
C&E |
Idea generation |
★★★★★ |
★★☆☆☆ |
Quantitative ranking |
★☆☆☆☆ |
★★★★★ |
Training burden |
Low |
Moderate |
Software need |
None |
Spreadsheet/QI tool |
Takeaway: Fishbone for breadth, Matrix for depth. Run them back‑to‑back and you have a full‑stack RCA.
Visual Tools for Root Cause Analysis: Comparing Fishbone, Flowcharts, and Cause & Effect Diagrams
Now that you have understood the concept of Cause and Effect vs Fishbone Diagram, let’s have a rapid tour of root cause analysis tools for visual problem‑solving approach. Five most commonly used quality control toolsare mentioned below:
Tool |
Best For |
Watch‑Out |
Process Flowchart |
Mapping sequence, spotting rework loops |
Can hide systemic causes if overly linear |
5 Whys Tree |
Drilling deep on a single causal chain |
Risk of “blame the operator” if data‑light |
Pareto Chart |
Frequency analysis of defects |
Needs reliable defect coding |
Scatter Plot |
Checking correlation (e.g., temp vs viscosity) |
Correlation ≠ causation |
Success & Effect Diagram |
Replicating best practices |
Often overlooked in fire‑fighting culture |
Decision Framework—Pick the Right Tool Every Time
-
Define the clock. < 1 day? Start fishbone. > 1 day? Add C&E Matrix.
-
Gauge data maturity. No numbers? Fishbone. Data lake? Matrix + scatter.
-
Assess audience. Operators love pictures; executives love weighted scores.
-
Match risk level. Compliance hit? Use the combo and document everything.
-
Plan the handshake. Always transition from qualitative brainstorm to quantitative proof.
10 | Where Software Steps In
Manual whiteboards work for process improvement—but digital EQMS platforms (Qualityze, for instance) accelerate the cycle:
-
Built‑in fishbone templates tie directly to NC/CAPA records.
-
Drag‑and‑drop C&E Matrix auto‑calculates scores and highlights top offenders.
-
Real‑time dashboards track corrective‑action closure versus ROI.
-
Audit‑ready export satisfies ISO 9001 and FDA 21 CFR 820 evidence needs.
Teams that switched from spreadsheets and other traditional quality improvement methods to integrated RCA modules as their defect prevention strategy cut investigation time by 35 % on average, according to internal user surveys (2024).
FAQs— Cause and Effect vs Fishbone Diagram
Q1: What is the difference between a Fishbone Diagram and a Cause‑and‑Effect Diagram?
Both names point to the very same graphic. “Fishbone” simply refers to the sketch’s spine‑and‑rib layout that resembles a fish skeleton, while “Cause‑and‑Effect” highlights its mission: chart every plausible cause that can trigger the focal effect (your problem statement). Think of “Fishbone” as the nickname, “Cause‑and‑Effect” as the job description.
(can we have an image here of Fishbone Diagram and Cause and Effect?)
Q2: Why is the Fishbone Diagram important for Quality Management?
• It channels free‑form brainstorming into tidy categories (the 6 Ms or 8 Ps), so meetings stay focused instead of meandering.
• It draws out hidden factors—shifts in ambient temperature, undocumented settings, human fatigue—that classic checklists often miss.
• By capturing causes on one page, it becomes the launchpad for data collection, hypothesis testing, and ultimately a defensible corrective action.
Q3: When should I use a Cause‑and‑Effect Diagram in problem‑solving?
Deploy it whenever defects or complaints keep popping up after quick fixes. If a straight 5 Whys trace stalls at “operator error,” pull out a C&E diagram to uncover upstream influences—training gaps, tool wear, or vague SOPs—that simple questioning may overlook. It’s especially valuable for regulated CAPAs, where auditors expect a structured hunt for all plausible roots, not just the obvious ones.
Q4: Are Cause‑and‑Effect Diagrams and Ishikawa Diagrams the same?
Yes. Kaoru Ishikawa first drew the diagram at Kawasaki Steel in the 1960s; over time, practitioners honored him by calling it the Ishikawa Diagram. Different label, identical tool.
Q5: How do Fishbone Diagrams help in Nonconformance and CAPA processes?
They turn a nonconformance report into a living map: each “rib” lists possible triggers tied to a corrective‑action task. The visual lets cross‑functional teams agree on ownership in a single meeting—Maintenance tackles Machine causes, QA owns Method, HR addresses Manpower. That clarity accelerates CAPA closure and satisfies auditors looking for cause‑to‑action traceability.
Q6: Can I combine a Fishbone and a C&E Matrix in one session?
Absolutely. Step 1: sketch the fishbone to capture every conceivable cause. Step 2: move those causes into a C&E Matrix, scoring each by severity, occurrence, and detectability (or any weighting you prefer). The combo keeps ideation fast and prioritization data‑driven—no more “loudest voice wins” decisions.
Q7: Which tool pairs best with 5 Whys?
The Fishbone. Use it to lay out broad cause categories, then run 5 Whys down the tallest “rib” (highest‑probability cause). That sequential drill‑down prevents teams from chasing rabbit holes and ensures each Why digs deeper into a single causal chain.
Q8: What software automates fishbone creation inside CAPA?
Cloud EQMS Software platforms such as Qualityze include drag‑and‑drop fishbone templates, built‑in 5 Whys prompts, and one‑click export to a C&E Matrix. Everything links back to the CAPA record, giving auditors real‑time proof of a closed‑loop investigation—no photo uploads of smudged whiteboards required.
Q9: How do we know a Fishbone Diagram actually solved the problem—not just documented it?
Validation happens in three steps: (1) Verify the root cause you selected by running a containment or pilot fix—if the defect rate drops in a statistically significant way, odds are you hit the right nerve. You can reconfirm by re-introducing the root cause and see if the problem resurfaces. (2) Monitor leading indicators (first‑pass yield, customer calls, scrap percentage) for at least one full process cycle; sustained improvement proves permanence. (3) Close the feedback loop by adding the verified cause, corrective action, and new control checks back into your SOPs and training modules. Qualityze automates this review by linking the Fishbone’s chosen root cause to a CAPA task with built‑in effectiveness‐check reminders, so nothing falls through the cracks six months later.
Q10: What makes Qualityze’s Fishbone module different from free templates or spreadsheet add-ons?
Unlike basic templates that stop at visual brainstorming, Qualityze supports a structured, traceable approach to root cause analysis. It enables teams to go beyond identifying potential causes. It embeds accountability, risk evaluation, and follow-up as a part of process to adhere with regulatory expectations and quality system requirements. This way, root cause analysis becomes a meaningful, integrated part of your continuous improvement strategy rather than just a standalone exercise.
Key Takeaways
As they say, choose the wrong root‑cause analysis tool and you’ll end up chasing the symptoms; choose the right one and you’ll pinpoint the root cause and identify the fix. You must analyze your business requirements thoroughly before choosing the right tool. Understanding the key concepts of Cause and Effect vs Fishbone Diagram is just a first step.
-
Fishbone = fast breadth.
-
Cause‑and‑Effect Matrix = focused depth.
-
Blend both for chronic, high‑cost problems.
-
Visuals accelerate buy‑in—and slash defect cycles.
-
Modern EQMS turns whiteboard sketches into audit‑ready evidence.
“Failure is the seed of success.” — Kaoru Ishikawa
Plant those seeds in the right soil—use the right tool at the right time—and watch scrap, delays, and customer complaints wither.
Share
The Start of Something Amazing.
Request Demo
Products
Industries
Company