Table of Content
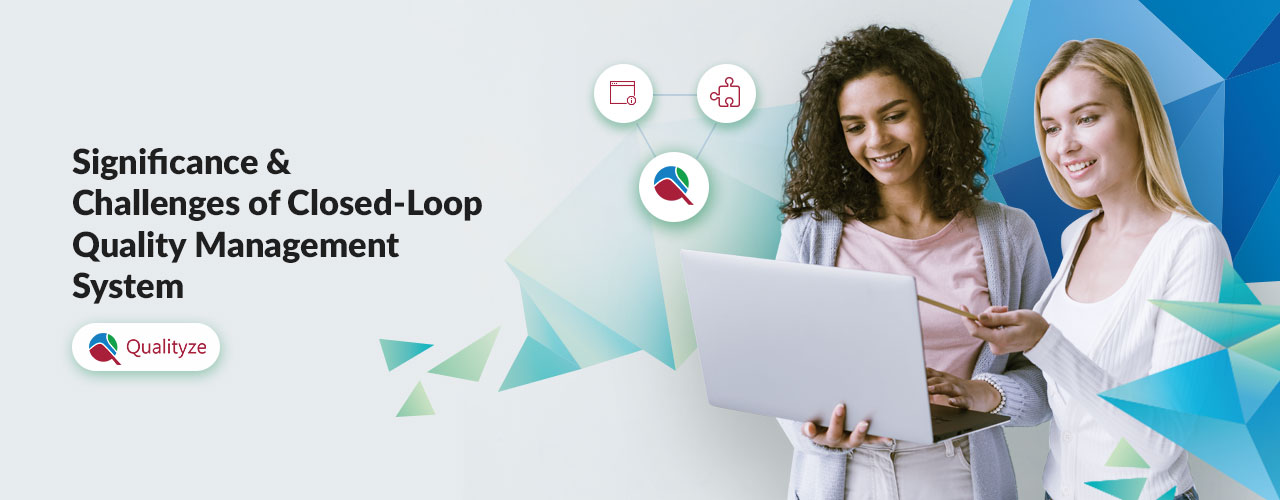
In the quality domain, it’s a common belief that sooner a nonconformance gets identified and resolved, lesser will be its impact. The advent of technology and cloud-based solution for quality management have made this belief even more actionable. The quality professionals can now have deeper insights and can make informed decisions with the use of closed-loop quality management system.
Especially when the next-generation solutions are making their way at such a faster pace – from designing, manufacturing, distribution, and marketing – industry leaders prefer to bring together the prominent data resources and systems that can form a closed-loop quality process between the key processes and the teams.
With such closed-loop processes, you can facilitate improvements in the existing quality management system for driving continuous improvement while reducing the overall quality issues and costs. Let’s first understand the term quality management system and closed-loop quality management in detail before moving to the discussion on its significance.
Quality Management System
A QMS refers to the collection of business processes that focuses on meeting customer requirements for enhanced satisfaction through consistent efforts. It is generally aligned with the organizational goals, ensuring that processes are streamlined in a strategic direction (ISO 9001:2015). It won’t be wrong to express QMS as organizational aspirations, goals, policies, processes, recorded and documented information, and the resources for the implementation and maintenance.
Earlier the quality management systems used to emphasize on predictable results for the production line by using the simple statistics and light sampling. Later in the 20th century, labor inputs became expensive especially in the industrialized societies, hence the focus shifted to teamwork and dynamics due to early signals of problems through continuous improvement cycle.
The 21st century brought QMS into the coverage of sustainability and transparency initiatives because both the investor and the customer’s satisfaction became the peak factors of achievement. Also, the ISO 9000 family of standards got widely implemented worldwide.
Closed-Loop Quality Management
The process of closed-loop quality management is basically about connecting the quality process across the organization regardless of the geographical differences so to meet the goal of improved quality. However, the connection may be established either in the same process as manufacturing or within the different areas/process like manufacturing and supplier quality.
Significance of Using Closed-Loop QMS
Most of the leading manufacturers now make a proactive approach to align their quality management processes with the business goals to eliminate the potential causes, which could result in bigger quality issues in the future. Such risk-based approach helps them prevent many of the problems that might not be identified until they reach manufacturing – or even worse – the end user experiences the functionality problems. With the implementation of risk-based approach keeping in consideration the analysis results, quality professionals can quickly determine the source of variations and proceed to the root cause analyses for resolving the quality issues, eliminating the time-consuming guesswork analysis completely.
Even the complicated and assembled products manufactured today are subject to risk-based engineering process to help the design and manufacturing teams to understand the critical dimensions clearly for developing a product exactly fitting to the requirements and quality standards. Even the product engineers use such approach before launching a product in the market.
This is not something new – a buzzword or revolutionary step. However, in a closed-loop quality management system, you can find multiple built-in steps that are defined to help product engineers in refining their plans and objectives quite early in the manufacturing process while keeping a regular check on ongoing activities to acquire the best quality for the customers within a minimum possible cost.
Challenges with Closed-Loop Quality Management Software System
Though closed-loop quality management system brings a significant improvement in product quality, it still needs to face certain challenges like:
No Commitment and Alignment from Top-Level Management
For maintaining a culture of effective quality management, there is a need for the organizational commitment that starts with the support of top-level management. Without their involvement, it is not feasible to make decisions, strategies, or implement new technologies for improving product quality. The processes will be rather dispersed as they will be created without taking organizational-wide operations in mind.
Keeping the senior management involved in the process also works as a support in building a streamlined quality culture in the organization that encourages employees to understand how their actions matter for the critical things including reduced cost of quality.
There are many organizations that are still facing this challenge. The main reason behind this challenge is an unaware workforce. The employees consider quality as a department, not as a responsibility. They are less likely to take ownership of quality specific functions. All they focus on is completing their end of duty or tasks assigned.
Short-Term Visions Around Business Processes
The big organization especially the ones who have expanded their business globally and indulged into M&A activities will considerably have different solutions for the same quality issues at a different location. Though they vary in terms of the business unit, division, plant, or geography, processes including audits, training, and CAPA, they have the same goal i.e. product quality. Consequently, they will suffer a lack of standardization. The regular M&A activities and indifferent approaches to quality comes up as the real serious challenge for the companies that are looking forward to closing the quality management loop.
A quality management survey conducted in 2012 revealed that 47% of the employees stated – they face challenges in closed-loop quality management process due to variances of data resources and quality systems. Also, there has been a massive use of manual processes to identify solutions for specific as well as local problems.
Nowadays, executives need to manage a lot of processes and solutions that require hefty of backend work merely to communicate the quality data properly. Hence, all the processes should be streamlined well across the organization regardless of the geographical differences. This will result in improved vision for the organization’s long-term goals.
Minimal or No Connection with Technological Architecture
Despite the variety of options of Enterprise Quality Management Software (EQMS) solutions, there are many organizations that don’t have automated, streamlined, standardized, and centralized platform for their quality functionalities. This grows worst with the challenge of diversified data resources and quality systems. And, the organizations that have distributed range are vulnerable to M&A activities, which simply adds to the complications of this challenge because they are supposed to have more than one enterprise applications running in the organization including ERP, CRM, etc.
As many of the processes are built in or on the top of them, diversified applications can often become a roadblock for the closed-loop quality management system. Instead of having a seamless solution that can facilitate real-time communication and collaboration, in many of the cases, the critical data can never be accessed at the enterprise level. Or, may be, they need significant resources including time and analysis to pull it to a point where it can be used for a substantial improvement in the process while changing a future decision.
Related Article - AS9100 - Aerospace Certification: Explained
Effective Quality Management with Closed-Loop EQMSs
Closed-loop quality management can serve as a key area to put more attention and investment for effective improvement in the quality of products, processes, and systems. if you want to add more strength to your organization’s quality management portfolio, you should get an EQMS like Qualityze that enables seamless integration to form a closed-loop quality management system for enhancing their quality capabilities and culture with improved IT architecture.
Qualityze is a powerful EQMS solution that enables market leaders to reap the advantages of communicative and collaborative capabilities to overcome every challenge that emerged as a major hurdle.
Stated above are the key challenges mentioned by the quality leaders. Are you facing some challenges with your current processes, and/or technology? You can let us know and our customer success team will be right there for you.
Share
The Start of Something Amazing.
Request Demo
Products
Industries
Company