Table of Content
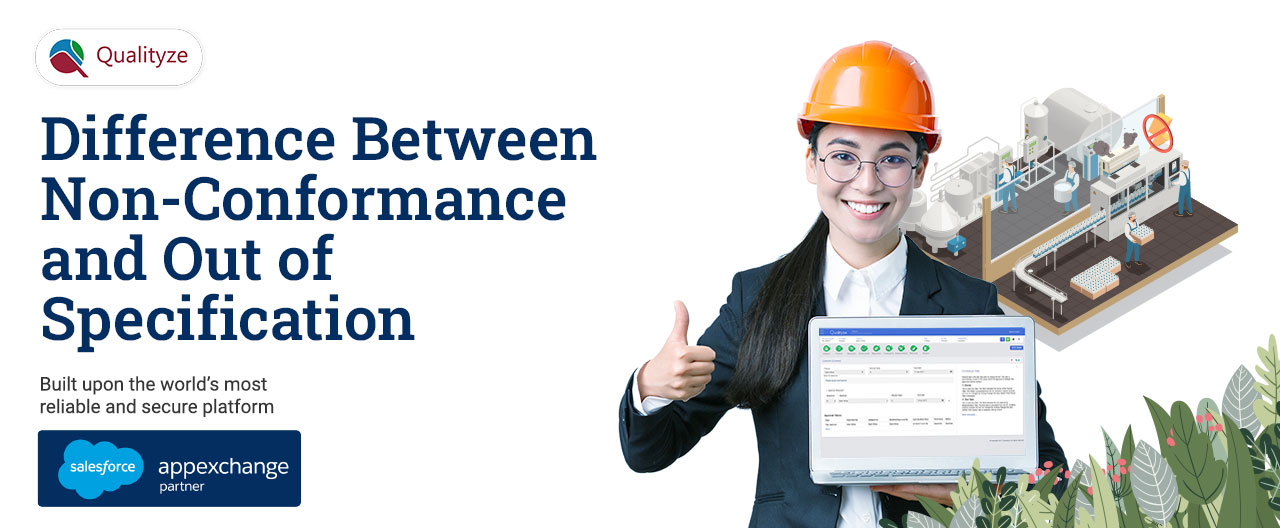
You may be involved in a highly regulated industry, such as medical devices, pharmaceuticals, biotechnology, or general manufacturing; companies whose control mechanisms fail to meet scientific standards cannot ensure that their testing protocols, products, containers, raw materials, or labeling will comply with the required standards of purity, identity, strength, and quality if they do not have scientifically sound controls. A mistake can result in adding the wrong concentrations of drugs, mixing the wrong drugs, or not using enough of a given drug. All of these are non-conformances.
But is it right to call nonconformances as out of specifications?
You may be thinking how are these different. In this blog, we are going to understand these terms and the key difference between the two.
Let’s quickly look at the definitions to start with.
What is a Nonconformnace?
Nonconformance is defined as a defect in a product specification, process parameter, record, or procedure. This defect causes the quality of the product to be unacceptable, indeterminate, or not in accordance with the specification.
Quick Read: Are Your Employees Filing Nonconformances Properly?
What is Out of Specifications?
Out-of-Specification (OOS) is when a sample’s results do not follow the industry’s standards. It may be that these criteria are compiled by an official reference resource set by your organization or that your testing lab sets them.
What’s the Key Difference Between Nonconformance and Out of Specification?
Though both the terms refer to the specifications that are not met, they are functionally different. When a nonconformance occurs, you may or may not conduct a detailed investigation to determine root cause of the problem. It depends on the risk severity of the issue -whether the nonconformance reported qualifies for CAPA or not.
On the other hand, when a product is out of specification, you must conduct an investigation to determine the root cause of the issue, regardless of its risk severity.
Another key difference that sets Nonconformance and Out of Specification is their dependency on the standard criteria. You may not have a specific criterion to categorize a quality issue as a nonconformance. Every quality issue is a nonconformance but to know whether it is out of specification too, you must evaluate it as per standard specifications for acceptable quality.
The source of nonconformance could be audits, routine testing, inspections, and negative feedback from customers. On the contrary, the source of out of specifications is generally the inspection team or quality assurance team who test the product at granular level. Your customers may not be able to figure out the products that are out of specification.
For example – A drug usually consists of different active and inactive ingredients in a specific dosage to serve the intended purpose. If the dosage of inactive ingredients is a bit more than the specified dosage, it can harm the consumer. The harm can sometimes be minimal and go unnoticed. In such a case, the nonconformance may not be reported.
The same issue, being identified by your quality assurance team, will be categorized as out of specification, and may impact the entire production. It can have even more severe consequences if the issue is identified at the regulatory inspections.
Whether it is a nonconformance or out of specification, quality issues must be handled proactively and timely to avoid rework, recalls, penalties, and other legal repurcussions. It may further harm the brand reputation and market share.
You must have a powerful system in place to report, manage, and track the quality issues identified. It will help you make better decisions, for example, if you really need to initiate CAPA for an issue reported. Or there is a need to perform production review to evaluate the impact of out of specifications.
Reporting and Managing Quality Issues: Which is the most reliable solution?
For managing quality issues in a standardized and compliant manner, you must implement a solution that enables you to establish best-practices workflows for the repeatable processes. It will reduce the overall administrative work associated with reporting and managing quality issues. Your teams will then have more time for resolving the quality issues and prevent their recurrence.
One such solution is Qualityze Nonconformance Management. With this solution, you can streamline your defect and deviation management processes by documenting, verifying, resolving, and investigating nonconformances, noncompliances, out of specifications, and deviations.
Qualityze Nonconformance Management seamlessly integrates with the CAPA Management Solution so you can thoroughly investigate the out of specifications and the issues with high-risk. The solution comes with advanced tools and impressive cloud capabilities to manage nonconformance in a timely manner.
The solution is highly configurable and intuitive. You can modify and configure the nonconformance reporting forms as desired to ensure consistent data inputs. The quality of inputs translates into intelligent decisions that drive continuous improvements and business growth. As a result, your brand reputation and market share will significantly improve.
To experience the Qualityze difference, request a free demo today!
For more information about Qualityze Nonconformance Management Software, feel free to reach our customer success team at info@qualityze.com, or you can call us at 1-877-207-8616, and we will be right there for you.
About Qualityze Inc
As a Next Generation Quality Management solutions provider, Qualityze helps enterprises address compliance, regulatory, and quality challenges. By aligning processes with quality objectives and strategic metrics, we help organizations achieve their goals. In addition, we provide Smarter Quality Solutions to improve organizations’ maturity and prepare them for competitive changes.
Utilizing industry best practices, standardized, repeatable processes, and easy-to-configure, predefined workflow templates, Qualityze Enterprise Quality Management helps you meet quality, compliance, and regulatory requirements. We provide a complete QMS solution with our integrated design.
With integrated analytics and reporting capabilities, organizations can analyze quality data in real-time, regardless of their industry focus. Involve quality teams in Reviews, Audits, Training sessions, Follow-up Tasks, Actions, Approvals, and Change Implementations as soon as possible.
With Qualityze, you can manage end-to-end quality processes from anywhere in the world, thanks to Salesforce.com, the world’s most secure and reliable platform. Transform your business with a quality decision-making engine.
Share
The Start of Something Amazing.
Request Demo
Products
Industries
Company