Table of Content
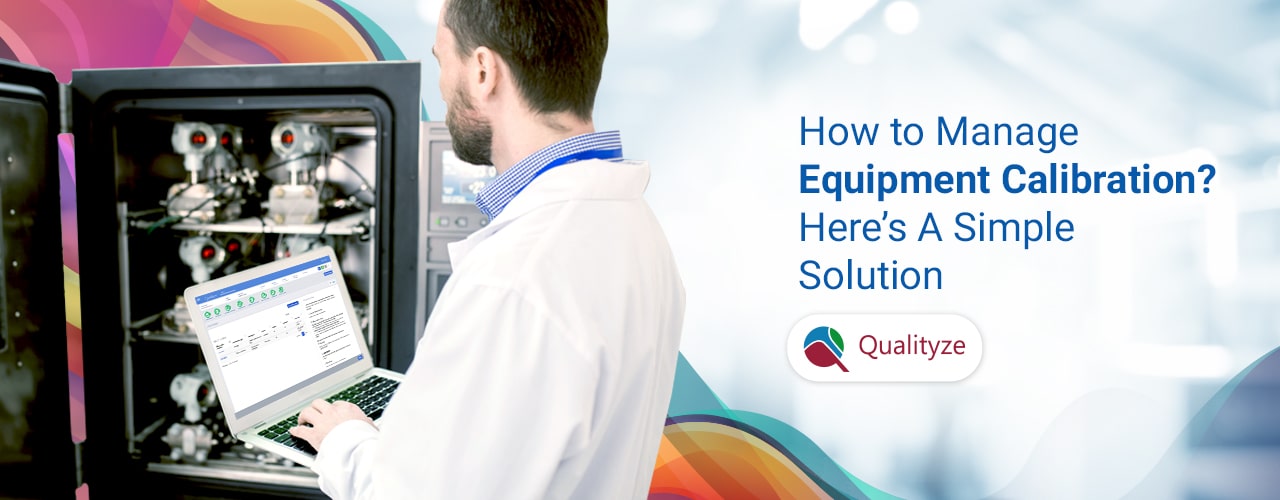
With the constant use and over time, there are chances of drift in any equipment’s performance. It can lead to measurement errors, which eventually will impact the quality of products and may even lead to catastrophic events. This is why; it is crucial to keep your equipment calibrated regularly.
But managing the calibration activities can be troublesome for enterprises since it involves multiple pieces of equipment from different company locations. If not managed properly, there will be possibilities of production downtime. It will further lead to delayed time-to-market.
The critical factor in managing equipment calibration is its frequency. If you can set the calibration frequency correctly, you are less likely to face production downtime or delays. Another critical aspect of calibration management is that “It is not one size fits all” thing. There are different types of equipment; so are their calibration requirements. Equipment calibration is done timely; you can significantly improve your equipment’s efficiency and performance.
Process of Equipment Calibration
Equipment calibration is one of the most effective ways to keep track of measurements’ accuracy and quality. The equipment measurements are generally compared with the standard values, which are accepted by the regulatory authorities. If any quality issue arises, the instrument is calibrated to provide accurate results within the acceptable limit and range.
It is even recommended in good manufacturing practices to focus on mitigating and reducing the factors that could lead to quality failures, inaccurate measurements, and nonconformances. Though all the equipment performs different functions and is calibrated differently, certain things are common, including:
- The Calibrators
They are validated and measured using the test instruments. You can find the test equipment for different devices, including the spectrum analyzer, oscilloscope, signal generator, logic analyzer, and much more.
- The Results
The calibration results are generally compared with the standard values.
- The Purpose
Calibration is basically conducted to minimize the measurements’ difference, if any. Once the equipment is calibrated, the instrument can measure any test samples with greater accuracy and precision.
- The Impact on Performance
Equipment calibration ensures better performance and equipment efficiency, ensuring zero compromises with the final product quality. Any equipment performs best when it is calibrated based on the manufacturers’ recommendations and compliance requirements.
Related Article : How to Manage Equipment Calibration
Specific Factors That May Impact Equipment Calibration
Equipment calibration is directly associated with its accuracy and efficiency. It is quite common to see shifts and drifts in equipment accuracy for multiple reasons, including time. Although calibration ensures that equipment keeps performing accurately, it is equally essential to ensure that calibration processes are conducted in the right environment where no other factors can impact it.
Yes, you heard it right. The overall environment can make or break the entire objective of the calibration process. Here are the factors that can disturb your calibration process:
- Incorrect values
Any equipment’s calibration shall be completed as per the standard procedure defined. If you choose the incorrect values or try to go against the standard procedure, it is likely to change the way equipment works. It may lead to many operation errors. Even the new equipment comes with an in-built alert system to notify the operators every time an incorrect value or measurement tests; it may be hard for them to identify the calibrators that are using the incorrect values. Therefore, you must be extra careful with the values you use.
- Inappropriate calibrator
Using the right quality calibrator is critical for the equipment calibration. So, you must use the calibrators that are certified and are manufactured by reliable labs or manufacturers. Enterprises need to understand that calibrators’ quality can directly affect the calibration results, which could lead to more significant problems. Using calibrators that have precise tolerances and specifications are highly preferable for consistent results and performance. Make sure to choose the right calibrators designed with the exemplary formulations, tolerance, and measurement for the particular equipment that needs to be calibrated.
- Environmental Conditions
As we have already discussed above, the environmental factors, including temperature and humidity, can significantly impact the calibrators and equipment. You must ensure that the equipment is calibrated in the environment within which they are going to operate. The minutest of the environment’s variations can result in a significant difference and fluctuations in the measurement.
How to Prevent the Factors as Mentioned Above to Impact the Calibration Activities?
Well, the only way to prevent the factors as mentioned earlier is diagnosis.
Here’s how?
When you perform the equipment diagnosis, you can quickly identify the equipment which needs to be calibrated and the ones that don’t need to be calibrated since not every piece of equipment needs to be calibrated at the same time. In fact, you should prioritize the equipment and devices based on their role in product quality and safety. The regular diagnosis helps your team categorize the equipment calibration frequency – whether it is good to go with periodic schedules or go with on-demand calibration.
You can also utilize the predictive maintenance software to gather crucial information. The same can be analyzed and tracked for identifying the measurement differences to initiate the calibration activity timely and prevent production errors and delays. Such control of the data and measurement information allows you to perform all types of calibrations quite efficiently.
Is It Time for Adopting Paperless Calibration Procedure?
It has been decades since the calibration tasks are managed manually. The calibration software has brought a revolutionary change by making the entire process paperless and automated. With the software, you can streamline and standardize the calibration processes, schedules, ad activities while keeping your data safe and secure on a centralized platform. You can access the required information anytime from anywhere across the globe and share it with the authorized people.
Making calibration software-based has helped organizations save money and time while preventing frequent downtimes. Gone is the time when the admirative staff used to spend most of their productive time in data entry jobs. The whole process has become faster, better, and smarter.
The software-based calibration management improves the overall quality and efficiency of the calibration process while leveraging multiple other benefits, such as:
- Automated and reduced calibration process cycles.
- Efficient management of the calibration-related data.
- Centralized calibration database can be instantly accessed in all the production units, regardless of their geographical locations.
- Seamless communication and collaboration with the quality teams.
- Paperless calibration management.
- Integration with existing quality systems to gain better control of calibration activities.
- Achieving compliance with applicable regulatory standards.
- Accuracy & Efficiency
Implementing an integrated calibration management solution like Qualityze provides a seamless experience in managing calibration activities while achieving three core things, including:
- Improved efficiency: With the next-generation calibration management solutions, the entire calibration process cycle can be simplified and streamlined, reducing production downtime. The software is fast and intuitive.
- Cost savings: With the automated software solutions, you can easily save a considerable amount of money effortlessly since it will eliminate the expenses like paper-based filing and storage systems.
- Improved quality: Calibration records are prone to errors when managed manually. The software has significantly improved the overall calibration quality.
Therefore, the best and simplest solution to manage equipment calibration is implementing the right calibration management software like Qualityze. It will completely transform the calibration process, making it faster and smarter.
Conclusion
The importance of equipment calibration cannot be underrated. It is the critical requirement for seamless production cycles and product quality. Whether scheduled or unscheduled calibrations, calibration management software are of great help to avoid any operational, production, and quality issues.
If you also want to know more about the cloud-based calibration management software and its benefits, get in touch with the Qualityze Customer Success team on 1-877-207-8616 or write us at info@qualityze.com, and we will be right there for you.
Share
The Start of Something Amazing.
Request Demo
Products
Industries
Company