Table of Content
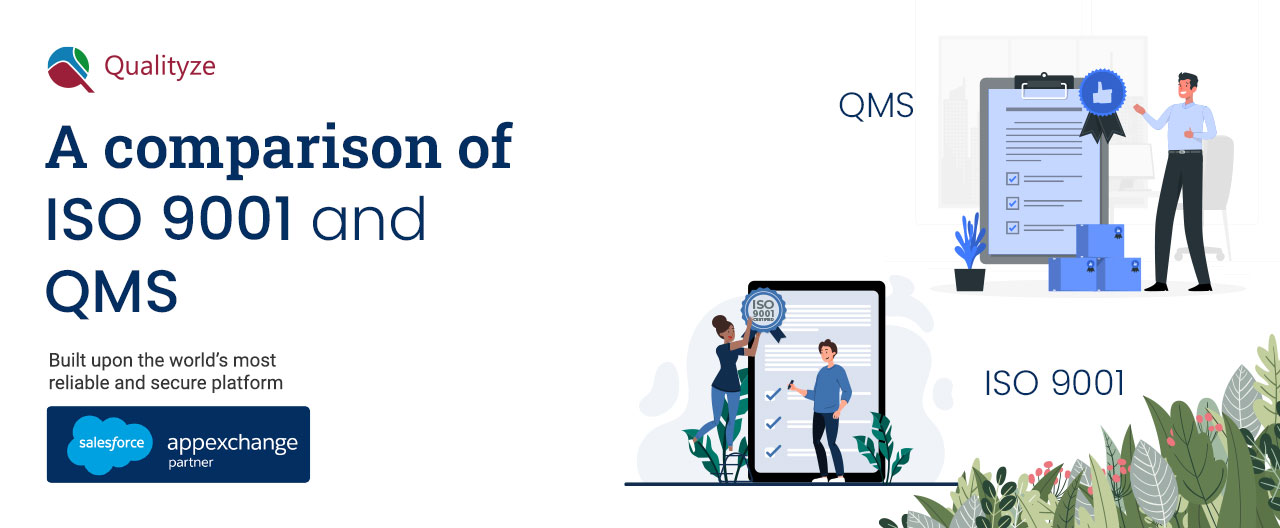
Businesses commonly standardize their processes. The standards in a particular field are highly distilled best practices developed by experts who understand the needs of their field. For example, a standard can describe how to create a product, manage a process, or deliver a service.
Historically, industry standards have been developed to enable organizations to align with external norms and provide their customers and suppliers with an understanding of their processes.
While several external bodies create standard systems, the ISO is the most commonly adopted. This is because it helps enterprises to make the most of their quality management system.
However, many enterprises consider both the terms the same. Here you will find out how ISO 9001 compares to quality management systems and how they differ.
Defining ISO 9001:2015
In ISO 9001, requirements are set forth for a quality management system (QMS) in an international standard. It demonstrates that a company can consistently provide products and services that meet client needs and regulatory requirements. Among the ISO 9000 standards, this is the most popular and the only one that can be certified.
Founded in 1987, ISO 9001 is an international standard developed by 160 national standards organizations from more than 160 countries. September 2015 marked the release of ISO 9001’s current version.
There is no industry or size restriction when it comes to ISO 9001:2015. The ISO 9001 standard is implemented in more than 160 countries by over a million organizations. ISO 9001 helps all types and sizes of organizations:
- Streamline and standardize processes
- Optimize processes to increase efficiency
- Continuously improve
With ISO 9001, organizations can consistently provide high-quality products and services to their customers, leading to higher customer satisfaction, employee satisfaction, and management satisfaction.
Organizations use ISO 9001 because it specifies the requirements for an effective quality management system so they can:
- Set up a quality management system
- Satisfy customers, employees, and management
- Continuously improve their processes
- Reduce costs
With ISO 9001, you get a framework to set up quality goals and achieve them on time. It defines all the best practices an organization can adopt to build a quality and continuous improvement culture. It also helps manage change effectively and efficiently so that change is no more considered a challenge in the business environment. Instead, it should be regarded as an opportunity to improve the quality, safety, and reliability of the products and services offered.
Since ISO defines the QMS requirements, let’s dig deeper to understand the quality management system and the associated processes. Knowing the processes involved will help you implement best practices more effectively than ever.
Defining Quality Management System
Quality Management Systems outlines how a company intends to produce quality products and offer quality services in compliance with regulatory requirements. An integrated quality management system can cover the entire lifecycle of a product or service by putting in place several quality management activities:
- Planning: ensuring all legal/regulatory requirements, as well as any customer requirements, are addressed.
- Quality Control: Establishing processes for ensuring consistent product quality
- Quality Assurance: Ensuring your product meets your customer’s expectations
- Improvement: Implementing changes to your processes and reviewing your output to ensure your standards remain high and that your customers are satisfied
It is crucial to document a QMS but not at the same time confuse it with the Management System. You can train employees and ensure they know what is expected during Quality Control by documenting your policies and creating process maps during the planning phase. The document contributes to both Quality Assurance and Improvement efforts as it provides a benchmark for measuring and reviewing the quality of a product or service.
In a QMS, the risk is considered regardless of whether the risks affect the quality of products or services. This includes failures to identify customer needs, comply with legal requirements, and maintain customer security, as well as failures in the quality of the products or services. Although partners or suppliers may be at fault for these failures, a QMS will address them and manage these issues.
ISO 9001 and QMS: How They Are Related?
It is pretty evident from our discussion above that ISO 9001 and QMS are closely related. Therefore, you must implement an ISO 9001 compliant quality management system to deliver superior quality products while meeting compliance.
However, an enterprise doesn’t need an ISO 9001:2015 certification to do business. It makes a more significant impact when they want to sell their products and services globally. So, if you want to start your quality journey, you can establish quality management processes in alignment with best practices without obtaining certification.
Once you are confident of the quality culture in your organization and want to scale your operations at a global level, you can apply for ISO 9001 certification.
ISO 9001 and QMS: Shared Goals
Although ISO 9001 and QMS are different yet closely related subjects, they share some common goals, such as:
- Ensuring quality, safety, and reliability of the products and services offered.
- Building a positive work environment.
- Ensuring customer and employee satisfaction.
- Establishing efficient processes for high-quality output.
- Improving brand reputation and market share.
Right EQMS Is All You Need
As stated above, ISO 9001 and QMS share some common goals. You can achieve them with the right approach, tools, and methodology. However, you might miss several opportunities if you are among businesses that still rely on paper-based systems or outdated technology.
It would be best to implement a next-generation, cloud-based enterprise quality management software like Qualityze. The software will help your teams to manage end-to-end quality processes on the cloud, enabling them to standardize best-practices workflows.
Highly configurable and intuitive, Qualityze EQMS Suite is delivered on the most powerful and secure platform, i.e., Salesforce.com. You can also leverage greater flexibility, security, scalability, and performance. It comes with a centralized database and many exceptional functionalities such as Digital Signature, Audit Trail, and Email Approval to ensure compliance.
Request a free demo today if you want to experience Qualityze difference in managing product and process quality.
To learn more about Qualityze products and their functionalities, feel free to contact our customer success team at info@qualityze.com or call us at 1-877-207-8616, and we will get back to you at the earliest.
Related Articles: Why Should You Invest in an Integrated EQMS Software?
Conclusion
ISO 9001 represents the set of QMS requirements, whereas a quality management system is a framework that binds all your quality processes together to produce high-quality goods. Aligning these together could be challenging with paper-based systems. Alternatively, it would be best if you use Enterprise Quality Management Software. It will help you achieve all your quality goals while meeting compliance and operational excellence.
Another benefit of the next-generation Quality Management Software is improved traceability since the cloud-based solutions provide a centralized database to securely manage all your quality records.
Would you like to experience the most simplified way of managing the quality process?
Share
The Start of Something Amazing.
Request Demo
Products
Industries
Company