Major Challenges Medical Device Industries face to Manage their Device Records
Table of Content
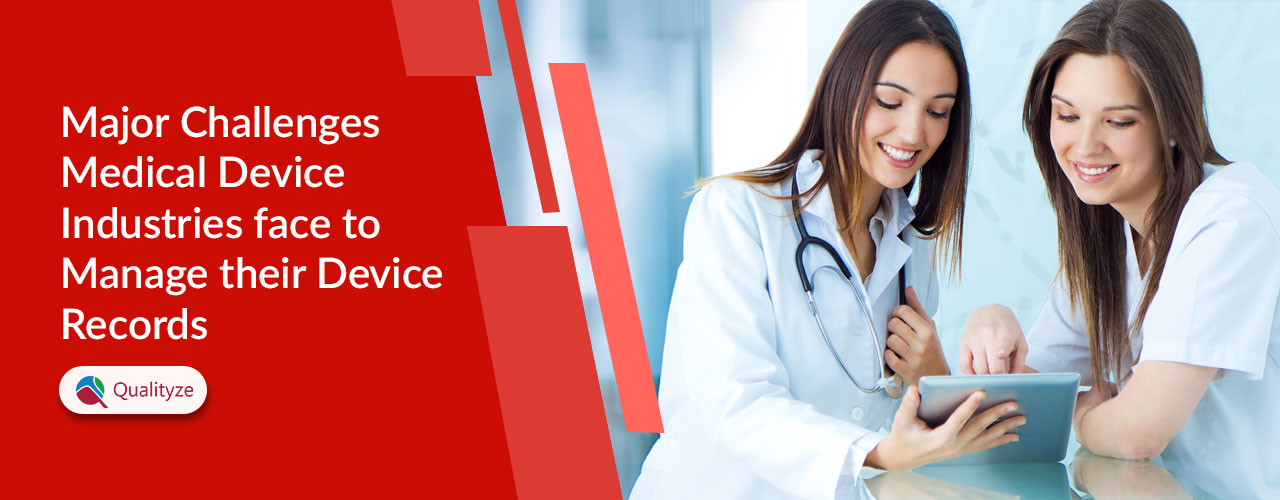
The medical device industry has witnessed tremendous growth in the past 10-20 years – in terms of revenues as well as the technical complexities of the product. There have been technological evolutions too in the medical device industry, but healthcare professionals still face many obstacles in meeting their goal of delivering quality care within an affordable range of the patients.
The major reason behind the obstacles is inappropriate management of information and device records. It’s high time for healthcare professionals to realize the need for an electronic document management system for maintaining Device Master Record (DMR).
A Quick Brief About Device Master Record
A Device Master Record refers to a collection of documents and records regarding medical devices including device specifications, packaging and labeling information, instruction for use, quality assurance procedures, and process specifications, which are mandatory under 21 CFR Part 820.181.
Process of Document Control in Medical Device Industry
In the highly regulated medical device industry, document control is one of the most important processes for the company’s success – in development and manufacturing. Maintaining the design and engineering records is essential to drive the development of medical products, and the Standard Operating Procedures (SOPs) is critical to governing how the business is done. You need well-organized, revision-controls, and easy-to-audit records for meeting the regulatory compliance.
In earlier times, companies used to create and update their critical data in the form of memos, SOPs, design programs, and spreadsheets. All the changes are then printed out and circulated in color folders to get signatures from the approving bodies. And the product information is usually communicated to the designated teams, outsourced partners like manufacturers and suppliers, and other authorities through call and email.
Moreover, the critical product records like the device master record (DMR), design history file (DHF), and bill of materials (BOM) are often stored in a combination of vaults, spreadsheets, and in paper-based files. All this is followed by the loading of final BOMs to the ERP systems.
All these factors, in addition to the stringent regulatory requirements, compressed product lifecycles, geographically dispersed project teams, cost savings, and the outsourced business partnerships, tend to become challenging for efficient document control and communication in many ways:
Complexity of Records
New-Age Product Records – including Design History Files, Device Master Records, and Bills of Materials- are huge, complex, and ever-changing. Trying to make and control the changes manually to the geographically dispersed teams through spreadsheets and other formats are vulnerable to errors and inefficient. This also makes it difficult for you to maintain compliance traceability mandated by several regulations.
A Large Amount of Data
Modern records are also relational. They include a variety of relevant data and files containing metadata and much more. For example, if we talk about the Device Master Records or Design History Files – they will be different for every products and part, then there will be many revisions reflecting the changes made over the lifecycle of the device. In addition, all the drawings must be synchronized with their links for easy tracking. Also, there will be compliance data that you need to attach with the records. Do you think that spreadsheets, on-site static servers, and paper files are efficient enough to offer an integrated way to bring all the related item data together?
Maintaining Records in a Validated State
As we have already discussed in the above point, the complexity of managing data in spreadsheets and servers, we should not forget the need for a validated state to keep both the components in function. And, it is quite a challenging job. Being business owners, you must be aware of the fact that every Device Master Record and Design History File must be available to the auditors at any point in time. You must retain and keep a back-up of your records for a set number of times that is mandated by the regulations. But spreadsheets are one of the fluid assets that cannot match the level of accountability that an organization needs especially in the medical device industry.
Related Article : What is a Quality Agreement and Why is it Important?
Inefficient Change Management Process
Traditional processes that include spreadsheets and ERP systems are not integral to manage engineering change orders (ECOs). Neither they can control the changes of device master record (DMR) and associated files, nor they can create proper documentation required by the FDA for the DHF because FDA regulations require proper verification, validation, review, and documentation of ECOs in every product’s DHF. Manual circulation of the paper ECOs through colored folders won’t be safe, sustainable, and efficient practice.
Managing Revisions of Product Information
In the complete lifecycle of a product, you are supposed to create several revisions of product information and communicate the same to the internal and external teams. Ensuring that everyone in your team is referring to the latest revision of the product information, especially when it is communicated through spreadsheets and paper-based files are almost impossible. It tends to be a bigger challenge when you want the current product data from your suppliers and partners.
Related Article : EQMS: Taking Biotechnology Quality to New Heights
Why Automated Document Management and Change Control Management Solutions are Better to Maintain the DMR?
Today automated solutions are available to help companies organize, maintain and communicate product information—including the device master record (DMR), design history file (DHF) and bills of material (BOM) —to succeed in today’s competitive environment for highly-regulated industries like Pharmaceuticals, Lifesciences, Automotive, etc. Organizations today need to accelerate the introduction process for their new products while improving collaboration with their suppliers and other outsourced partners to meet compliance standards with confidence.
A recent study by Aberdeen Group reveals that most of the best-in-class companies outperform significantly well than stragglers when it comes to new product development. Such companies leverage advanced tools to improve their overall performance and profitability. There are more than 50% of companies that are likely to leverage the centralized product repositories for better use of core information by capturing, sharing, and reusing the things like bills of materials (BOMs).
If you want to have an organized structure to manage all your critical documents and their relevant changes, you should choose Qualityze Change Control Management Solution. It is built on Salesforce.com and offers complete flexibility and scalability to grow along with your business.
You can also invest in Qualityze Enterprise Quality Management Solution through which you can control all your quality management activities in a single solution.
From documenting nonconformances to performing root cause analysis for adequate CAPA actions, from creating compliance-friendly documents to manage their changes in a validated system, from training your workforce to training and managing your suppliers’ quality, and from managing audits to managing customer complaints to unleash new growth opportunities, Qualityze serves it all.
This powerful software comes with truly beneficial features and capabilities like Outlook Email Approval, Electronic Signature, Alerts and Notifications, Dashboard, Audit Trail and much more to ease your quality management processes while mitigating the operational risks. Qualityze enables you to have a closed-loop quality management system to manage your quality needs based on compliance and customer requirements.
Would like to know more about Qualityze EQMS Software? You can simply call us on +1-877-207-8616 or email us at info@qualityze.com. Our customer success team will get in touch with you. You can also request a free demo to experience next-generation capabilities in real-time, and you will also get 1-week free trial.
Share
The Start of Something Amazing.
Request Demo
Products
Industries
Company