Table of Content
1 What is a Non-conformance in Manufacturing?
2 Why Address Non-Conformance?
3 Types of Non-Conformances in Manufacturing
4 Importance of Managing Non-Conformance in Manufacturing
5 Preventing Manufacturing Non-Conformances
6 Examples of Non-Conformances in Manufacturing
7 Managing Non-Conformance with Qualityze
8 Parting Shot
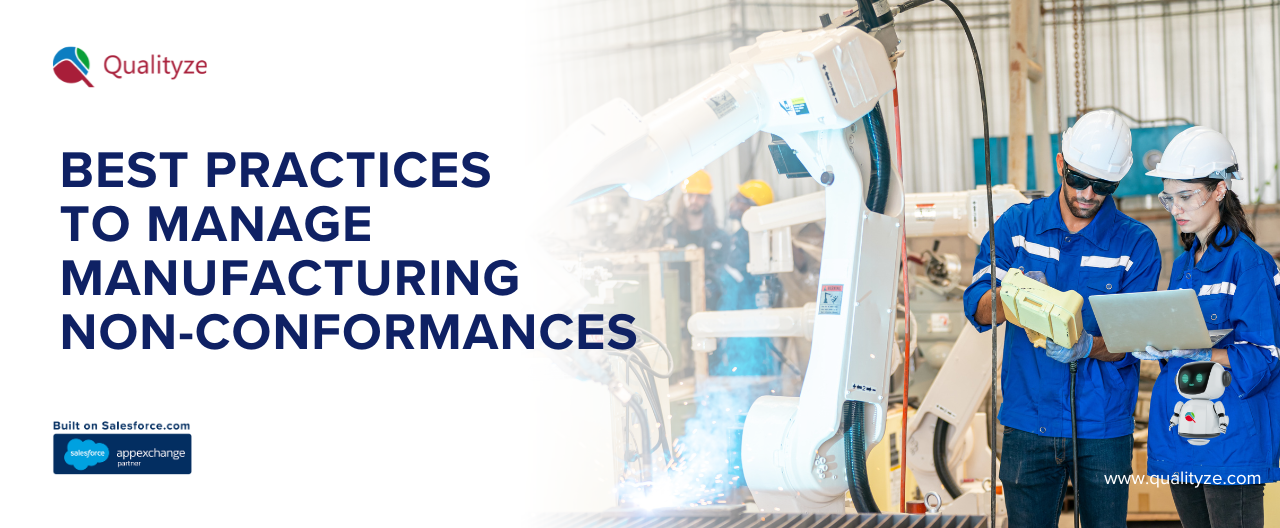
A non-conformance is a deviation from your specified requirement. It means a product or process doesn't meet your quality standards. Violation of quality standards could range from minor issues like a missing label to major defects that compromise safety or functionality.
Manufacturing Non-conformances can lead to costly reworks, compliance issues, and low product quality. Addressing non-conformance issues quickly, cost-effectively, and efficiently is crucial to maintaining operational efficiency and compliance with industry standards.
Qualityze's Non-Conformance Management Software module provides a solution to identify, document, and resolve non-conformances while helping manufacturers modernize their processes and maintain compliance.
This blog spotlights best practices for managing non-conformances and how an automated process can empower your organization to effectively manage non-conformances for maximum benefits.
What is a Non-conformance in Manufacturing?
Non-conformance in manufacturing refers to any deviation from established specifications, quality standards, regulatory requirements, or a company's internal SOPs. When a product, process, or material fails to meet a set standards, it is classified as non-conforming. Non-conformance can arise due to various factors, including human error, equipment failure, inadequate procedures, lack of employee training, or material defects.
Managing non-conformances is critical to prevent quality issues, customer dissatisfaction, and regulatory penalties. Each instance must be recorded, analysed, and corrected to avoid recurrence, and helping you to achieve consistent quality and regulatory compliance outcomes.
Why Address Non-Conformance?
Failing to manage non-conformances can have long-term effects on production quality, customer satisfaction, and regulatory compliance. Manufacturers need to focus on identifying, assessing, and correcting non-conformance issues to consistently deliver high-quality products.
Types of Non-Conformances in Manufacturing
Manufacturing non-conformances are generally categorized as:
- Product Non-Conformance: Product non-conformance refers to products that do not match quality standards or specifications. These issues could result from design flaws, raw materials, user error, incomplete testing, or mishandling during assembly.
- Process Non-Conformance: Process non-conformance happens when the manufacturing process deviates from the prescribed steps or quality standards. This can stem from equipment malfunctions, operator errors, or inaccurate measurements.
- Documentation Non-Conformance: Arises from not following the Good Documentation Practise which, often leads to misunderstandings, compliance risks, or quality issues.
- Supplier Non-Conformance: Results from supplier-provided materials or components that fail to meet specified quality standards, impacting downstream processes.
- Material Defects: Material non-conformance occurs when raw materials do not meet the required specifications. This could result from supplier issues, incorrect material handling, design issues, or a flaw in the storage process.
- Design Flaws: Design errors can cause recurring non-conformances, harming a brand's reputation and causing financial losses due to recurring errors.
- System Non-Conformance: System non-conformance is due to failures in quality management systems or procedures. Inadequate documentation, lack of training, or outdated protocols can lead to system-level non-conformances.
By classifying non-conformances, companies can implement a targeted corrective action to eliminate risks and improve overall quality.
Importance of Managing Non-Conformance in Manufacturing
Managing non-conformance is essential for several reasons:
- Regulatory Compliance: Industries such as Medical Devices, Pharmaceuticals, automotive and aerospace are strictly regulated. Non-conformance incidents can lead to penalties and harm the company's compliance status. Manufacturers can avoid legal repercussions and uphold compliance obligations by managing non-conformances effectively. Non-conformances must be documented and resolved to ensure compliance with regulatory standards such as ISO, FDA, etc. Failure to address non-conformance issues can result in fines, recalls, and loss of certifications.
- Product Quality: It ensures products meet quality standards and customer expectations, eliminating or minimizing the cost of customer acquisition.
- Brand Reputation: A strong reputation for quality can attract and retain customers.
- Cost Efficiency: Non-conformance management helps reduce rework, waste, and recall costs. A proactive approach to non-conformance can also prevent issues from escalating, saving time and resources.
- Customer Satisfaction: Delivering consistent high-quality products boosts customer trust and satisfaction. Addressing non-conformance quickly ensures customers receive reliable products, reducing the likelihood of complaints or returns.
- Continuous Improvement: Managing non-conformances effectively provides valuable insights into possible process weaknesses and opportunities for improvement. Companies can enhance quality control measures and implement continuous improvement practices by tracking and analyzing non-conformance data.
Preventing Manufacturing Non-Conformances
Preventing non-conformance is integral to a quality-driven manufacturing process. Here are some key steps:
- Implement Standardized Processes: Manufacturers should establish clear quality standards and operating procedures. Detailed guidelines help employees understand expectations and minimize process deviations.
- Implement Root Cause Analysis (RCA): RCA helps manufacturers understand the underlying causes of non-conformance incidents. By addressing root causes, companies can prevent the recurrence of similar issues.
- Implement Robust Quality Control Systems: Implement rigorous quality control measures to identify and address potential issues early.
- Employee Training: Training ensures that employees understand quality standards and their roles in maintaining compliance. Educated staff are more likely to detect non-conformance issues and follow proper protocols to address them.
- Supplier Quality Control: Evaluate suppliers and set quality benchmarks to avoid downstream issues with non-conforming materials.
- Regular Audits and Inspections: Conduct routine audits to detect deviations early and implement corrective actions promptly. Routine inspections of equipment, materials, and products are crucial to identify potential non-conformance issues early. Regular checks help catch defects before they progress further in the production process.
- Use Statistical Process Control (SPC): Use tools to monitor and control the manufacturing processes.
- Utilize Quality Management Software: Qualityze’s Non-compliance management software builds quality into every step of production, reducing the cost of product recall and rework. Real-time tracking, data analysis, and automation streamline the process, allowing manufacturers to catch issues before they lead to non-conformance.
Examples of Non-Conformances in Manufacturing
Here are some common examples of non-conformance in manufacturing:
- Process Deviations: Failure to follow prescribed processes leads to product quality inconsistencies.
- Documentation Errors: Missing or inaccurate documentation leads to compliance issues and production errors.
- Cosmetic Defects: Visible defects like scratches or dents.
- Incorrect Labelling: Products with incorrect labels or missing information.
- Dimensional Defects: Deviations from specified dimensions in a product or component, often leading to assembly issues or functional limitations.
- Material Defects: Issues arising from substandard materials affect the final product's durability and performance.
- Functional Failures: Products that do not function as intended.
Managing Non-Conformance with Qualityze
Qualityze's EQMS Software of Non-Conformance Management helps manufacturers manage and eliminate non-conformances efficiently:
- Automated Non-Conformance Reporting: Qualityze NC software management enables automated reporting of non-conformance issues, allowing for swift documentation and analysis. Automated reporting minimizes manual errors and ensures that all incidents are recorded with consistent details. The capture software captures essential data, analyzes trends, and identifies, potential challenges.
- Configurable Review and Approval Processes: Qualityze's Non-conformance management software enables customized review and approval processes, ensuring each non-conformance meets the specific requirements and internal SOPs of a company's compliance standards. This feature improves transparency, making the process visible to all stakeholders involved.
- Audit Trails for Traceability: Qualityze maintains a comprehensive audit trail for all non-conformance activities, recording who performed each action and when traceability ensures accountability and enables flawless audits by demonstrating consistent, compliant, non-conformance management practices.
- Mobile Accessibility: Qualityze's mobile-friendly platform enables remote teams, allowing employees to report, track, and resolve non-conformances from anywhere. This feature ensures teams respond promptly to quality issues, improving incident handling and overall response times.
- Compliance Support: Qualityze’s Non-compliance management software heps companies adherence to industry standards like ISO 9001 and GMP.
- Real-Time Data and Reporting: Qualityze's platform provides real-time access to data and customizable reporting options, allowing manufacturers to monitor quality performance metrics and detect patterns in non-conformance incidents.
- Seamless Integration with Existing Systems: Qualityze Non-compliance management software integrates seamlessly with ERP, CRM, and other enterprise systems. Integration streamlines data flow across departments, enhancing collaboration and visibility.
Parting Shot
Tracking non-conformances is a critical aspect of manufacturing operations. By following best practices and utilizing advanced software solutions like Qualityze EQMS Suite, businesses can effectively identify, address, and prevent non-conformances, ultimately improving product quality, customer satisfaction, and regulatory compliance.
Effective management of non-conformance in manufacturing is essential to maintaining product quality, meeting regulatory requirements, and protecting brand reputation. Manufacturers can enhance their quality processes by implementing best practices and utilizing tools like Qualityze's Non-Conformance Management to prevent recurring issues and drive operational efficiency through tracking, tracing and trending issues using the latest quality tool, such as Qualityze.
Share
The Start of Something Amazing.
Request Demo
Products
Industries
Company