Table of Content
1 Why Quality Strategy Matters in 2025
1. The Compliance Landscape is Changing Fast
2. The Cost of Non-Compliance is Rising
3. Quality = Business Success (Not Just Compliance)
5 The Changing Landscape of Quality in 2025
Why Playing Catch-Up on Compliance is a Dangerous Game
The 2025 Regulatory Shake-Up: What You Need to Know
What This Means for You
9 The Shift: From Reactive to Proactive Quality Strategy
10 Your Next Steps: How to Implement a Future-Proof Quality Strategy in 2025
Step 1: Audit Your Current Quality & Compliance Processes
Step 2: Choose the Right Tech-Stack for Automating Quality and Compliance Processes
Step 3: Integrate AI Without Disrupting Operations
Step 4: Get Rid Of Implementation Challenges
Step 5: Measuring Success & Proving ROI
16 Final Thoughts: The Future of Quality is Here
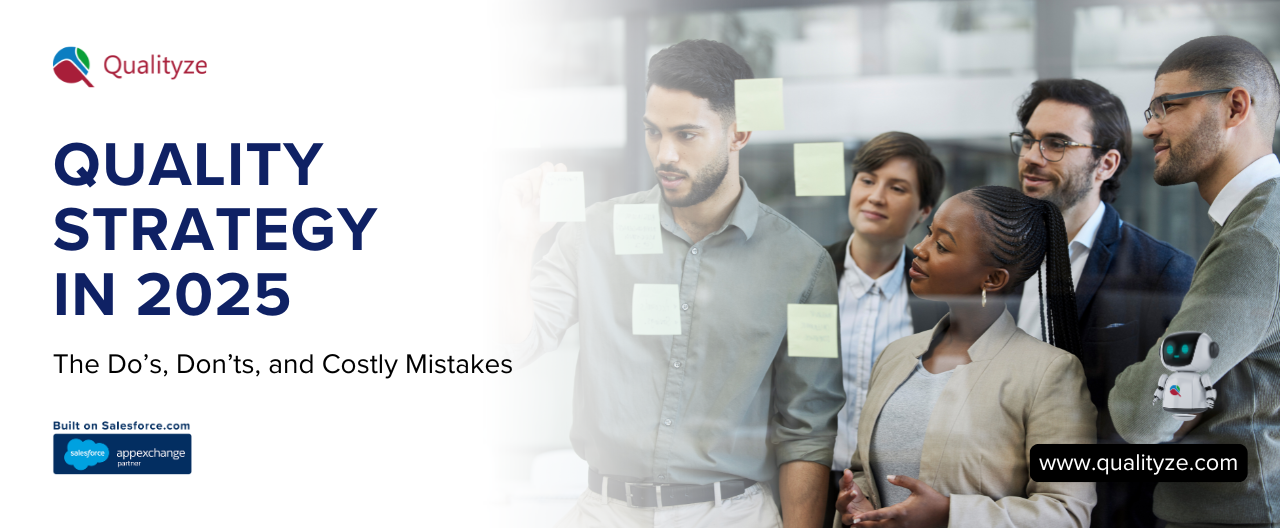
You know what’s worse than an FDA warning letter?
Finding out about it on the news before your own team tells you.
Sounds dramatic? It happens more often than you’d think.
Take the case of a well-known pharmaceutical giant (We won’t name names, but you can guess). They had been "managing" quality issues internally fixing problems on the go, keeping records just enough to pass audits, and hoping their batch failures wouldn't raise too many eyebrows.
Then reality hit.
A surprise FDA inspection exposed undocumented deviations, incomplete batch records, and failures in supplier quality management. The fine? $500 million. The recall? Even bigger. The impact on their reputation? Priceless… in the worst way possible.
Lessons Learned: ‘Cutting Corners in Quality is the Fastest Way to a Crisis.”
Now, contrast that with another company—same industry, same regulations—but a radically different approach.
Instead of treating compliance as a burden, they saw it as a competitive advantage. They built a future-proof quality strategy with automated compliance tracking, AI-driven risk assessment, and proactive supplier quality management.
The result?
-
Zero recalls in five years.
-
Audit-ready at all times.
-
Millions saved in compliance costs.
That’s the difference between reactive and proactive quality management.
And that’s exactly what this blog will help you achieve.
Why Quality Strategy Matters in 2025
If you’re reading this, chances are, you already know that quality isn’t just about compliance.
It’s about staying ahead of risks, reducing costs, and ensuring business longevity.
But here’s the kicker: 2025 is going to be even tougher on compliance than previous years.
New regulations. Higher standards. Stricter audits.
If you think the EU MDR shakeup was intense, wait until you see what’s coming.
Here’s why you need to rethink your quality strategy today:
1. The Compliance Landscape is Changing Fast
Governments and regulatory bodies aren’t playing around anymore.
-
The FDA is ramping up AI-driven inspections (yes, they’re using AI too).
-
The EU MDR & IVDR updates are catching companies off guard.
-
Global supply chain issues are forcing tighter supplier controls.
2. The Cost of Non-Compliance is Rising
In 2023 alone, FDA warning letters skyrocketed. Companies paid millions in fines, faced product bans, and saw their brands destroyed overnight.
And we haven’t even talked about lawsuits.
A single recall or compliance failure can set you back years in lost revenue and reputation.
3. Quality = Business Success (Not Just Compliance)
Let’s be real. No company ever dominated its market by just "meeting minimum requirements."
The best companies in pharma, medical devices, manufacturing, and food & beverage go beyond compliance.
They turn quality into a competitive advantage by:
-
Automating compliance (because paperwork is so last decade).
-
Using AI to predict quality issues before they happen.
-
Building supplier relationships that reduce risk and improve efficiency.
And guess what? Their profit margins are higher because of it.
Basically, if you’re serious about compliance, efficiency, and building a business that doesn’t crumble under regulatory pressure, you will find real value in this blog.
The Changing Landscape of Quality in 2025
Why Playing Catch-Up on Compliance is a Dangerous Game
Most companies don’t think about compliance until they absolutely have to.
They wait until an audit is around the corner. They scramble when a regulatory update drops. They react when an issue blows up.
And by then?
It’s too late.
What if, instead of playing defense, you owned the game?
Because 2025 isn’t just another year for quality management—it’s a turning point. The rules are changing fast, and if your organization isn’t adapting, you’re setting yourself up for a painful wake-up call.
Here’s what’s coming.
The 2025 Regulatory Shake-Up: What You Need to Know
No matter what industry you’re in—pharma, medical devices, food & beverage, manufacturing, automotive—compliance requirements are getting more aggressive.
🚨 FDA is Raising the Stakes
-
AI-driven inspections: The FDA is using AI to analyze risk patterns and flag high-risk companies before they even schedule an audit.
-
Stricter supplier accountability: New FDA rules demand deeper traceability across the supply chain. If your supplier fails, you fail.
-
More frequent enforcement actions: The number of FDA warning letters and recalls is skyrocketing. The message? Comply or pay.
🚨 EU MDR & IVDR: No More Gray Areas
-
The transition periods are ending, and enforcement is ramping up.
-
Expect more stringent post-market surveillance requirements and heavier documentation burdens.
-
Companies that aren’t fully compliant risk losing their EU market access.
🚨 ISO 9001 & ISO 13485: Stronger Focus on Risk-Based Thinking
-
Regulators now expect organizations to proactively identify, assess, and mitigate risks before they turn into problems.
-
More rigorous internal audits will be required to maintain compliance.
-
Companies without robust risk management frameworks will struggle to pass certification renewals.
🚨 Global Supply Chain Disruptions = Tighter Quality Controls
-
With ongoing supply chain instability, regulators expect companies to have better supplier oversight—no excuses.
-
Real-time visibility into supplier quality performance is now a necessity, not a luxury.
-
Companies relying on outdated supplier tracking methods are at high risk for compliance failures.
What This Means for You
Let’s break it down:
❌ If you’re still managing quality with spreadsheets and manual processes
You’re going to fall behind.
❌ If you only focus on compliance when an audit is coming up
You’re putting your business at risk.
❌ If your quality data isn’t centralized and accessible in real-time
You won’t have the insights you need to stay ahead of issues.
On the flip side:
✅ Companies that embrace AI, automation, and proactive risk management will dominate.
✅ Organizations that integrate quality into their business strategy will see compliance as an advantage—not a burden.
✅ Businesses that invest in real-time quality visibility will avoid costly fines, recalls, and disruptions.
Which side do you want to be on?
The Shift: From Reactive to Proactive Quality Strategy
Regulators aren’t just looking for companies that check the boxes anymore.
They want companies that are:
✔ Risk-focused – Identifying and addressing compliance risks before they turn into violations.
✔ Data-driven – Using AI and automation to streamline compliance and improve efficiency.
✔ Audit-ready 24/7 – Not scrambling last-minute, but maintaining a state of continuous compliance.
✔ Digitally transformed – Moving beyond paper-based QMS to cloud-based, AI-powered quality systems.
Your Next Steps: How to Implement a Future-Proof Quality Strategy in 2025
So now you know AI and automation aren’t just trends—they’re the key to staying ahead in compliance.
But here’s the real question:
How do you implement this in your company?
Because let’s be honest—digital transformation in quality management isn’t as simple as flipping a switch.
It takes a clear roadmap, the right tools, and buy-in from leadership to make it work.
Step 1: Audit Your Current Quality & Compliance Processes
Before you start upgrading your systems, you need to get a clear picture of where you stand today.
Here’s how to do it:
🔍 Evaluate your existing QMS:
-
Is it manual or digitized?
-
Are there siloed quality processes?
-
Can you access real-time quality data?
-
Are compliance tasks automated or still handled manually?
📊 Identify gaps in compliance & efficiency:
-
Where do audits take the most time?
-
What are the biggest sources of quality issues?
-
Are suppliers meeting your compliance standards?
🚀 Set goals for digital transformation:
-
Reduce audit prep time by X%
-
Improve CAPA resolution speed by Y days
-
Increase supplier quality performance by Z%
Step 2: Choose the Right Tech-Stack for Automating Quality and Compliance Processes
Not all QMS and AI solutions are created equal.
The wrong system? It will slow you down.
The right system? It’ll transform your compliance process.
Here’s what to look for when choosing compliance automation tools:
🔹 1. Cloud-Based EQMS with AI Integration (like Qualityze EQMS Suite)
-
Real-time data access from anywhere
-
Automated workflows for CAPA, audits, and supplier management
-
Seamless integrations with ERP, PLM, and training systems
🔹 2. AI-Powered Risk & Compliance Monitoring
-
Predictive analytics to flag quality risks before they happen
-
Automated root cause analysis for CAPA management
-
Smart document control to eliminate manual compliance tracking
🔹 3. Supplier Quality & Risk Management Tools
-
AI-based supplier scoring for performance tracking
-
Real-time risk alerts for high-risk suppliers
-
Integration with regulatory compliance databases
🔹 4. Audit-Readiness & Regulatory Reporting Automation
-
Auto-generated compliance reports for faster audit prep
-
Digital signatures & audit trails for FDA & ISO compliance
-
Configurable dashboards for tracking key compliance metrics
Step 3: Integrate AI Without Disrupting Operations
One of the biggest fears about AI adoption? Disrupting daily operations.
But here’s the thing—AI should enhance your workflows, not replace them.
How to Integrate AI Without Chaos:
✔ Start Small: Implement AI in one high-impact area first (e.g., CAPA, audits, supplier risk management).
✔ Ensure System Compatibility: Choose AI tools that integrate with your existing QMS system and ERP.
✔ Train Teams Gradually: Focus on hands-on AI training for quality teams before full deployment.
✔ Pilot AI on a Small Scale: Test AI in a single department or process before rolling it out company-wide.
Step 4: Get Rid Of Implementation Challenges
🚧 Challenge #1: Resistance to Change
Solution: Get leadership buy-in & train teams early on why AI improves efficiency.
🚧 Challenge #2: Data Migration Issues
Solution: Use AI-driven tools that automatically clean, organize, and migrate existing quality data.
🚧 Challenge #3: Choosing the Wrong Software
Solution: Test drive multiple AI-QMS solutions before committing. Look for user-friendly, scalable options.
🚧 Challenge #4: Compliance Concerns
Solution: Work with regulatory experts to ensure AI-powered compliance tools meet FDA, ISO, and EU MDR requirements.
Step 5: Measuring Success & Proving ROI
How do you know if your AI-powered compliance strategy is working?
You measure it.
📊 Key Metrics to Track:
✔ Audit Readiness Score → How quickly can you pass an inspection?
✔ Time Saved on Compliance Tasks → How much manual work has AI replaced?
✔ Cost Savings on Compliance Management → How much money are you saving?
✔ Defect & Recall Reduction Rate → Has AI-driven risk prevention reduced product issues?
✔ CAPA Investigation Time → Has AI improved root cause identification & resolution?
Final Thoughts: The Future of Quality is Here
In 2025, compliance isn’t just about meeting regulations—it’s about optimizing efficiency, reducing costs, and building a quality-first culture.
Companies that embrace AI, automation, and proactive compliance management will lead their industries.
Companies that don’t? They’ll struggle to keep up.
Now it’s your turn.
Are you ready to transform compliance into a competitive advantage?
Is your organization prepared for AI-powered quality management?
Will you be audit-ready 24/7—without the last-minute panic?
The future of quality is already here.
The only question is: Are you ready to lead it?
If you want a personalized consultation on AI-driven compliance or looking for an expert-led demo on automation & quality?
Let’s talk. Book a strategy call today.
Share
The Start of Something Amazing.
Request Demo
Products
Industries
Company